Overview
Section 150 of the Work Health and Safety Regulation 2017 (NSW) requires that electrical equipment is regularly inspected and tested by a competent person if the electrical equipment is:
"...used in an environment in which the normal use of electrical equipment exposes the equipment to operating conditions that are likely to result in damage to the equipment or a reduction in its expected lifespan...".
All items of electrical equipment at UTS should be assessed for the degree of risk they present and control measures put in place to manage that risk.
Supervisors of work areas having electrical appliances must ensure that:
- electrical appliance risk assessments are performed to determine what requires inspection, test and tagging and how frequently
- inspection, test and tagging is conducted in their area of control on those items determined to require inspection, test and tagging.
A competent person is one who has acquired skills and knowledge to carry out the task through qualification, knowledge or experience.
At UTS inspection, testing and tagging of electrical equipment is performed by either:
- a suitably qualified contractor engaged to test and tag electrical equipment
- a UTS staff member who has completed the national unit of competency: 'Conduct in-service safety testing of electrical cord assemblies and cord connected equipment' or equivalent, or
- a licensed electrician
Contact David Lloyd-Jones in Safety & Wellbeing for information on selecting a contractor to perform testing and tagging of electrical equipment or access to electrical safety training.
Precautions
Electrical appliances
- Use the correct appliance for the specific task.
- Ensure that electrical appliances are dry and clean.
- Do not use general purpose electrical appliances when wet or in wet areas without suitable safety switches (always push-button test the residual current device before each use).
- Keep loose cables off the floor.
- Do not:
- withdraw a plug from a socket by pulling the cable;
- attempt to replace faulty lamps in light fittings
contact UTS: Facilities Management for assistance; or - overload power boards with electrical devices
contact UTS: Facilities Management if you require extra power outlets.
Extension cables
- Extension cables should only be used as temporary tools.
- Avoid the use of extension cables along walkways and corridors.
- Safety switches should always be used with extension cables.
Electric heaters
- Heaters are not to be used in air-conditioned spaces.
- Electric bar heaters should not be used - fan heaters with thermostats and timers are recommended.
Risk management
Step 1: Identify the hazard
Identify items of plug-in electrical equipment in your area that may require regular inspection and testing.
Electrical equipment in a hostile operating environment, extension leads and power boards (EPODs) should be inspected and tested. Residual current devices (RCDs) should also be tested regularly.
Hostile operating environment
is defined in the Work Health and Safety Regulation 2017 (NSW) as one in which the normal use of the equipment exposes the equipment to operating conditions that are likely to result in damage to the equipment or a reduction in its expected life span, including conditions that involve exposure to moisture, heat, vibration, mechanical damage, corrosive chemicals or dust.
Electrical equipment risk assessment and inspection record
List these items in the electrical equipment risk assessment and inspection record, download the template:
Electrical equipment risk assessment and inspection record template (Word, 45 Kb)
Step 2: Assess risk
Develop a test / inspect / tag protocol based on risk assessment.
Determine how often each item requires testing based on level of risk from the above template. Some particularly high-risk items may regular 6 monthly inspections. Some items require less frequent inspection or just formal visual inspection (e.g. equipment rarely moved or NOT in a hostile operating environment). Some items may not require testing or inspection at all (e.g. fixed equipment, office equipment and equipment that is never moved).
Choose a colour combination of tags for alternating years e.g. orange and green. Red tags signify failed items.
Step 3: Controlling the risk
Perform testing according to your test protocol.
Items must be tagged to show when they were inspected and by whom. Failed items must be tagged as unsafe and removed from service.
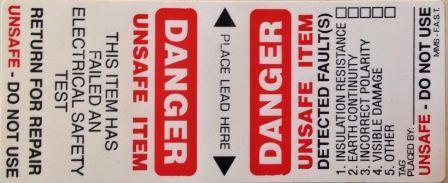
Only a competent person should perform testing and inspection of electrical equipment.
For further information of Electrical Testing and Tagging click here (UTS Staff access only).
Resources
Australian Standards / New Zealand Standards
- HB94-1997 Electrical Safety in the Workplace
Australian Standards
ISBN 0-7337-1136-7 - AS/NZS 3760:2022 - In-service safety inspection and testing of electrical equipment
State government legislation
- Clause 150 of the Work Health and Safety Regulation 2017 (NSW) (opens an external site)
- Electricity (Consumer Safety) Act 2004 (NSW) (opens an external site)
WorkCover Authority of NSW
- Electrical safety (opens an external site)
Safe Work Australia
- Draft code of practice: Managing electrical risks at the workplace (opens an external site)
training.gov.au
- Unit of competency details: UEENEEP026A - Conduct in-service safety testing of electrical cord connected equipment and cord assemblies (opens an external site)