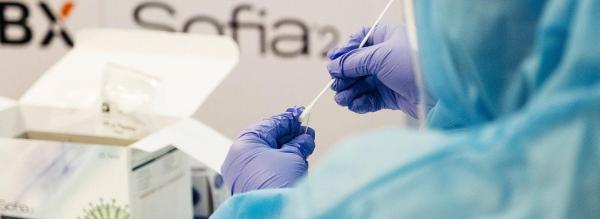
Testing times – ensuring PPE’s effectiveness in low-income countries
During a pandemic, Personal Protective Equipment saves lives – but only if does what the manufacturer says it will. UTS engineers are working with not-for-profit Field Ready and colleagues in-field in Kenya, Iraq, Bangladesh and Uganda to ensure its efficacy.

Sophie Ritchie,
Social Impact Manager, Rapido,
Faculty of Engineering and IT
Profile page
In the world of manufacturing, dodgy operators aren’t new, but as the world struggles to come to grips with COVID-19, it’s more important than ever that they are called to task.
‘It’s simple. Testing life-saving medical products is incredibly important – it saves lives,’ explains Rapido Social’s social impact manager, Sophie Ritchie.
But developing countries can struggle to meet the strict requirements set by standards bodies for testing, she explains, even outside of times of crisis.
‘Without standardised testing practices, especially of medical devices and equipment, products that do not reach the requirements to protect lives can slip through the cracks. In the current crisis, anyone could be selling masks to protect from COVID with the claim that they have the same safety specifications as an n95 surgical mask.’
As third and fourth waves of COVID-19 are make themselves felt around the world, there is clearly an urgent need for practical and easy to implement solutions. Sophie believes the Social Impact Grant funded collaboration between Rapido Social and Field Ready, could make a real difference.
THE SOLUTION
It may not look like much – a barrel connected by a recycled hose to a plastic base – but this Rapido Social prototype can be used to check face shields are actually blocking the infectious droplets produced when patients cough, sneeze, talk or even breathe, especially in small or cramped spaces.
It also comes with a set of instructions: CAD drawings and a step-by-step guide to construction and use that can be used by engineers, medical workers and others in the field.
So far, Rapido Social equipment drawings and guides have been shared with in-country engineers in Kenya, Iraq, Bangladesh and Uganda. The team has also developed similar drawings and instructions for machines to test face masks.
To do so was not without its challenges. Development required a constant back-and-forth between Kate Leone and Rebecca Carrucan – mechatronic engineers at UTS’s city campus in Sydney – and their Field Ready colleagues and local representatives overseas. Together they determined which materials and technologies to use and how best to swap-out components for those most accessible in-country.
WHERE TO FROM HERE?
Field Ready creates practical solutions to some of the world’s most pressing problems – ensuring that the tools most needed in crises can be made in-country by locals for minimal cost and to high standards. It’s a natural fit for Rapido Social, a UTS centre that aims to use cutting-edge engineering and technology to bring about lasting positive social change.
The collaboration is only just starting to bear fruit, but the longer-term impact of the work done has the potential to be profound, says Sophie.
‘Standardised testing procedures are often very technical and complicated and require machines that cost millions of dollars. Many countries are reliant on imports or simply cannot accurately verify equipment’s effectiveness. I hope our work increases access to tested COVID PPE that can save lives. Longer term, I hope that it also paves the way for cheaper and easier-to-manufacture testing methodologies and practices for other medical devices as well.’
The Problem
Testing PPE requires materials and equipment that are often not readily available in many low-income countries. Many can struggle to meet the strict requirements set by standards bodies for testing.
The Response
Rapido Social teamed up with not-for-profit Field Ready to create CAD drawings and instructions to build PPE testing equipment so it can be rapidly manufactured on-the-ground in countries that most need it.
What helped accomplish this?
The partnership with Field Ready and discussions with in-field engineers helped establish what was – and what was not – possible in different countries. The project also received funding from the Centre for Social Justice & Inclusions Social Impact Grant scheme.
What has changed as a result?
So far, testing equipment drawings and guides to construction and use developed for the project have been shared with in-country engineers in Kenya, Iraq, Bangladesh and Uganda.
Download full case study