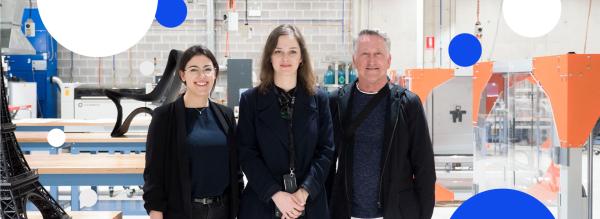
Creating prosthetic limbs out of recycled plastic
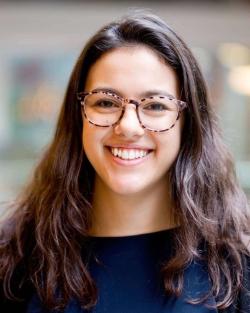
Kate Leone, Associate Mechatronic Engineer, Engineering and IT Solutions, Rapido
Profile page
Every year the world produces 380 million metric tonnes of plastic waste, a whopping 91 per cent of which isn’t recycled. But breakthrough Rapido Social research could help turn the tide, changing the lives of two kids in Queensland in the process.
3D printing is a kind of modern-day alchemy.
Creating automotive components, jewellery and even body parts by ‘printing’ them from designs readily available online has become, if not exactly child’s play, then certainly an enthusiastic hobbyist’s dream.
“Typically, in the case of FFF (Fused Filament Fabrication), a.k.a. FDM, you’re laying down plastic layer by layer and it looks like a slug of melted goo but then when it cools you can see whatever it is you’ve plugged in – a test cube, a tool or even something as complex as an architectural model,” says Kate Leone, a mechatronic engineer at UTS’s Rapido Social and recipient of $10,000 in 2019 Social Impact Grant funding.
“Almost anyone can use the technology. It’s irrelevant who they are and what technical background they have – you can buy a printer now for under $500,” she says.
This potential for everyday use means 3D printing has applications beyond creating cheaper, lighter components for industry, Kate explains – it can also help us to think in new ways about recycling plastics.
High-density polyethylene (HDPE) is common. Used for everything from shampoo bottles to milk crates, it’s estimated that over 50 million metric tons of it are created worldwide every year. It is also non-toxic and so is approved for medical use by the US Food and Drug Administration (FDA) – a characteristic that attracted Rapido Social, which seeks to leverage cutting-edge engineering and new technologies for maximum social benefit.
“We worked with Bernie Craven, CEO of Waste Free Systems and an ex-hairdresser, who noticed an abundance of waste in salons – the majority of shampoo and conditioner bottles are made from HDPE,” explains Rapido Social’s social impact manager, Sophie Ritchie. “But we also built a relationship with the not-for-profit e-NABLE who release open source designs online so that 3D-printed prostheses are more accessible.”
Shredding plastic from shampoo and conditioner bottles then melting them down into long ‘spools’ of filament from which to create prosthetic components on a 3D printer had its challenges. While recycled HDPE is medically safe, it is renowned for being temperamental when heated and extruded onto a printer bed – it shrinks as it cools and has a hard time sticking (and thus layering) in one spot.
Yet the project team were able to achieve some remarkable results – from an initial shrinkage rate of about 12 per cent, which resulted in warped and unusable objects, they were able achieve shrinkage of less than 0.5 per cent in test cubes, paving the way for future research to increase recycled HDPE use in 3D printing.
The team also contributed to the open-source prosthetics space, redesigning a 3D-printed hand to improve its mobility. The new design enables users of the artificial hand to move and orient their fingers in ways not previously possible – pivoting from a mechanical wrist to change from the vertical position needed to hold a pen to the horizontal one required to hold onto a bike’s handlebars.
“This project was an exciting opportunity, because it enabled us to explore solutions for two difficult social issues at once – the excess of waste plastic globally, and the cost-barriers to purchasing prosthetic limbs,” says Sophie.
“The team also donated prostheses to two Queensland kids – Connor and Haley,” says Kate. “When the cost of an artificial limb can be anywhere between $5000 and $50,000, this is a real game changer for these families. It’s really satisfying.”
The Problem
Globally, 380 million metric tonnes of plastic are produced each year – very little of which is recycled. Traditional prosthetic limbs are costly and too expensive for many who need them most. Plans for cheaper open-source 3D-printed artificial limbs are available online but can have limitations.
The Response
Rapido Social experimented with 3D printing of recycled plastic to produce components for prostheses – overcoming significant technical barriers to using recycled HDPE and developing new concepts for 3D-printed hands to allow users, including children, to more easily do things like ride a bike.
What helped accomplish this?
Close relationships were developed with Waste Free Systems, a not-for-profit that recycles HDPE used in hairdressing salons, and e-NABLE – an online community that reduces the cost of artificial limbs by providing a platform for open-sourced 3D-printable prosthetic designs.
What has changed as a result?
The project team were able to overcome one of the main problems when using recycled HDPE in 3D printing – warping cause by shrinkage. This paves the way for further research to increase recycled plastic use in 3D printing in future. Concept designs were also created to improve the mobility of current 3D-printed prosthetic hands. Two kids from Queensland are set to receive artificial hands developed out of the project.
Download full case study