3D printing technology helping disabled refugee children
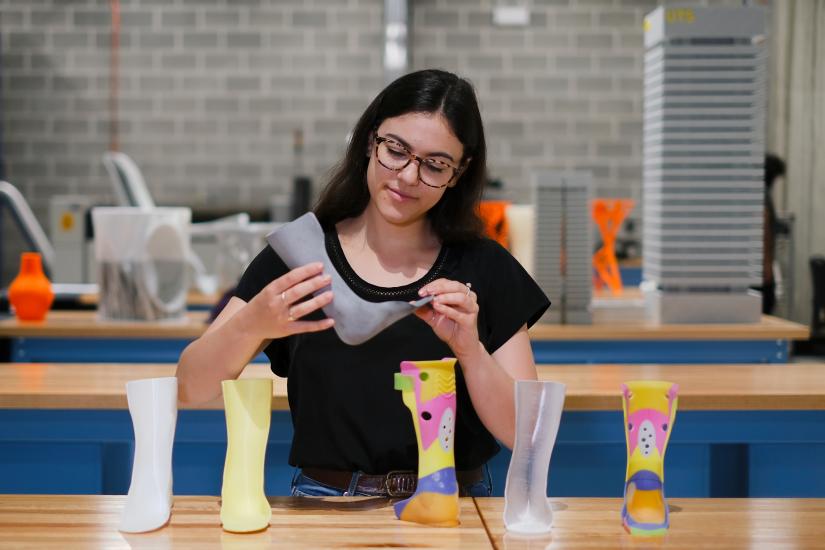
Mechanical and mechatronic engineering student Kate Leone holding a 3D printed ankle-foot orthosis.
Every 15 hours, an Australian child is born with Cerebral Palsy. Most of these children require the use of orthoses, which, worn at critical developmental milestones, can be the difference between walking and not walking.
Globally, 100 million children need orthotics and demand is exponentially outstripping the supply of the orthotists who make them. This can lead to wait times of up to 12 months just for an appointment, and doesn’t even take into account the time it takes to make the product itself. Once the child finally gets an appointment with an orthotist, the method of plaster casting the child can be slow, messy and traumatic for the child and their families.
Without access to orthotic services, people are often confined to their homes and excluded from participating in society, locking individuals into a cycle of poverty and isolation.
These compounding issues, paired with a desire to help people with disabilities access the equipment they need, inspired UTS Rapido Social and for-purpose tech company AbilityMade to partner up to revolutionise the orthotics sector with 3D printing.
“The idea for this project came from a dire need for innovation in the orthotics sector to meet the demands of the community that requires them,” said Sophie Ritchie, Social Impact Manager at Rapido Social.
“AbilityMade’s mission is to tackle the shortcomings in the current provision of ankle-foot orthoses (AFOs) such as turnaround times, discomfort and cost – and Rapido Social has partnered with the organisation to help them achieve this end.”
Rapido Social is a subdivision of UTS Rapido, a Faculty of Engineering and IT (FEIT) Research and Development (R&D) Unit established to deliver technological innovation for social and industry impact.
AbilityMade are a for-purpose tech company that develops products to promote mobility and accessibility for people of all abilities.
“Rapido Social and AbilityMade have known about each other for a while, being that we are both working in the tech for social impact space,” Sophie said.
“We first came into contact with AbilityMade when a mechatronic engineering student we were supervising, Kate Leone, undertook a research project comparing various materials and 3D printing technologies for the fabrication of AFOs, on behalf of AbilityMade.”
“That first collaboration with AbilityMade was such a success and we knew that we wanted to work with them again. We wanted to take R&D in the area to new heights,” she said.
That opportunity came in 2018 when the Rapido Social team received a Social Impact Grant from the UTS Centre for Social Justice and Inclusion. With this funding, which was also matched by their faculty, Rapido Social and AbilityMade began work on their new collaborative project.
“The objective of this project was two-fold. Firstly we wanted to drive innovation in the area through the design and development of an automated fatigue testing machine for 3D-printed AFOs. Secondly we wanted to be able to give the AFOs we printed to some of Australia’s most disadvantaged children, that is, children from refugee backgrounds,” Sophie said.
During the process of printing an AFO, material and mechanical testing is done on a ‘dog-bone’ shaped test piece to ensure the strength, stiffness and yield of the material is up to standard. The data collected from these tests however, cannot accurately find the fatigue of the material, which determines how it will cope when subjected to fluctuating conditions, stresses or strains. Therefore, additional testing for fatigue must take place on a separate machine.
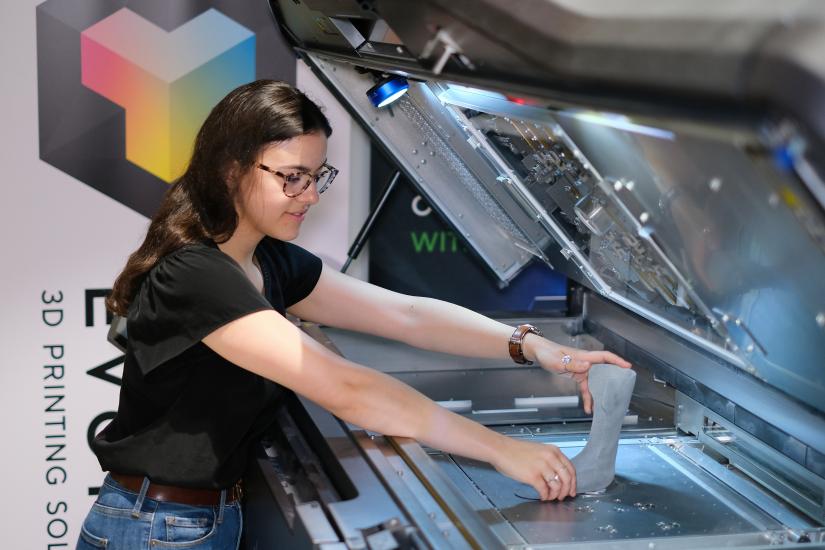
Kate Leone using a HP Jet Fusion 4200 machine.
Kate Leone, the engineer who drove the technical delivery of the project, set about developing a method of fatigue testing AFOs.
“The fatigue is important to test”, Kate said, “as it is representative of the lifetime of an AFO.”
“There are no existing off-the-shelf fatigue testing machines for AFOs. The previous rig that was being used by AbilityMade was a completely manual machine. By designing and building a completely automated version using motors and sensors, the testing can be considered more reliable. This proves to orthotists and patients that the 3D printing solution works just as well, if not better, than the old handmade AFOs.”
For Kate, seeing this new machine in action was one of the standout moments from the project.
“Turning on the automated fatigue testing machine for the first time with an AFO fastened in place, and it working without a hitch, was definitely a highlight.”
Once the initial testing has taken place, a 3D image of the child’s foot and ankle is taken with AbilityMade’s ‘instantaneous scanner rig’. The AFO is then modelled by in-house engineers in computer-aided software using the 3D scan. The model is then sent to be printed using a 3D printer at the UTS ProtoSpace.
Time-wise, it only takes a few minutes for the operator to input the data. The printing itself takes a maximum of 16 hours, with cooling taking a further 24. Final processing, including sandblasting and hydro dipping, then occurs. The AFO is then ready to go to the person who needs it most. This is a huge time saver when compared to the three to four weeks it can take for a traditional plaster cast AFO to be made.
“As a direct result of this project, there is capacity for us to print up to 10 AFOs for children in the Northcott refugee program,” Sophie said.
“This program established by Northcott Innovation in collaboration with Refugee Health NSW and AbilityMade, aims to provide 3D-printed AFOs to children with disability who have recently come to Australia as a refugee.”
While this project has now come to an end, Sophie said Rapido Social are definitely interested in working with AbilityMade again.
“We’re always looking for more ways to work with them. This project was very well received and supported by our peers in FEIT, and seems to have opened the eyes of many to the impact that engineering and innovation can have when applied to social justice matters.”